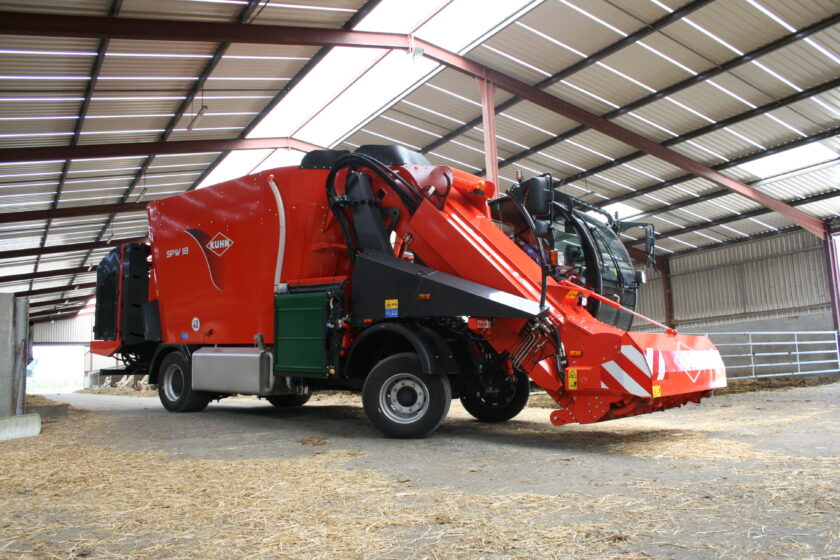
Italian beef and dairy cattle farms are undergoing a transformation. While the absolute number of farms is
decreasing, the average number of animals per farm is increasing. This trend is leading to a gradual decline
in less structured farms, often those with lower levels of technology, in favor of larger organizations
capable of optimizing the cost-to-revenue ratio through investments in both mechanization and per-capita
production efficiency. This assertion, particularly concerning dairy cattle, is supported by data published by
the European Commission. In Italy, the number of dairy cows decreased from 1,822,000 in 2015 to
1,639,000 in 2020, a ten percent decrease in just five years. According to Istat, the National Institute of
Statistics, this downward trend continued in the following two years, with Italian dairy herds decreasing to
1,631,000 heads by 2022.
Leading the regional rankings is Lombardy with 579,000 head, followed by Emilia Romagna with just under
252,000, while Veneto closes the podium with around 148,000 head. The top five also includes Piedmont,
just over 143,000 head, and Trentino-Alto Adige with nearly 90,000.
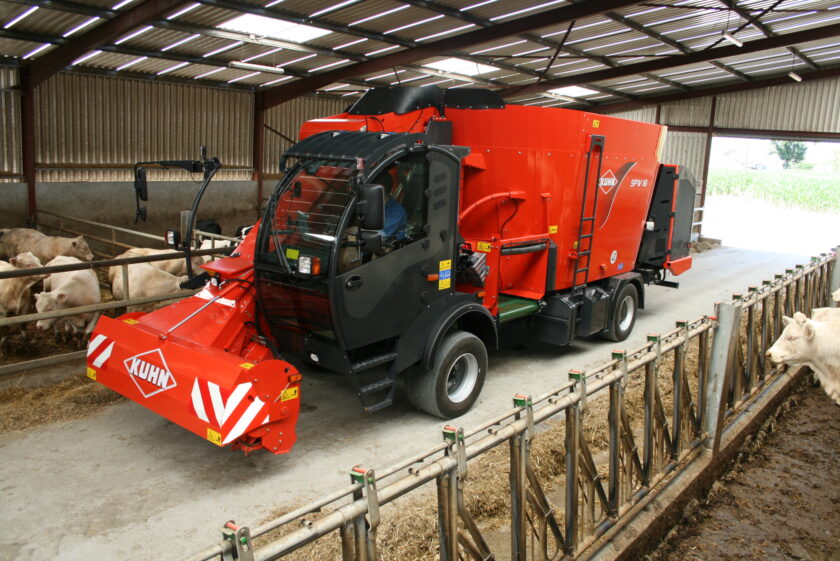
In 2022, Northern Italy as a whole held
78 percent of the total cattle in Italy, with the aforementioned five regions accounting for 74 percent of the national total. Looking at Lombardy, the leading region in the sector, the average number of heads per farm
was around 80, but within the so-called Lombard livestock triangle represented by the provinces of
Cremona, Mantua, and Brescia, the average consistency rose to 160 heads per farm. This implies that there
are still marginal farms with only a few dozen heads per barn, but it is increasingly difficult to remain in the
market even with potentially attractive milk prices, a situation that has yet to come.
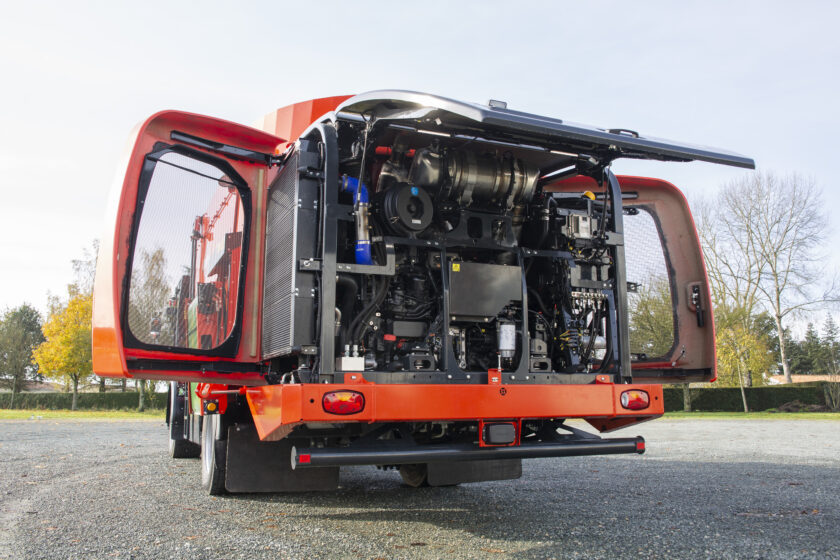
The concentration of heads is therefore confirmed to lead to higher efficiency levels, directly measurable at
milking. Referring to April, usually the month with the highest productions, there is a significant increase in
per capita volumes recorded in 2014 compared to those recorded in 2021: in just eight years, the average
daily milk production increased from 30.8 kilograms to 34.4 kilograms, an increase of over three and a half
kilograms, or 11.7 percent. This was followed by an equally significant increase in the average days of
lactation, from 186 to 195 units. In the same period, another interesting datum is the increase in the
percentage of cows with average milk productions exceeding 40 kilograms. If in April 2014 only 17.2
percent of the heads exceeded this threshold, in April 2021 this percentage had risen to 28.3 percent, an
increase of 11.1 percent, consistent with the increase in average milk production.
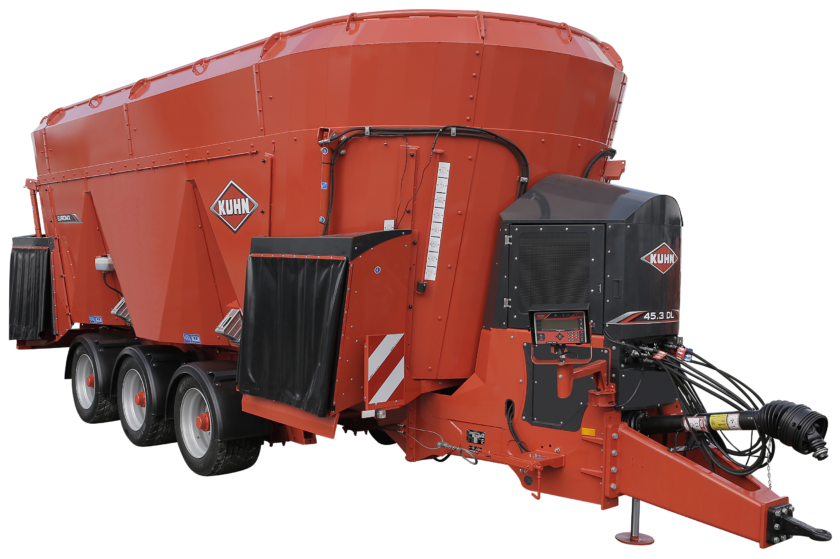
In essence, the overall productivity of a farm has been driven by the ability of individual animals to produce
more, a return induced by the refinement of nutritional techniques and an increasingly scrupulous
application of animal welfare regulations. To fully exploit nutritional advances and properly balance rations,
it is necessary to also increase the efficiency of the equipment used to prepare and administer the rations,
leveraging innovative technologies offered by leading machine manufacturers. Two examples in this regard
are the mixing wagons available from Kuhn in self-propelled or trailed versions, providing various technical
solutions to meet different farm needs.
Among the self-propelled mixers, the “Spw Intense” series stands out, consisting of seven “heavy-duty”
models with volumes ranging from a minimum of 14 to a maximum of 27 cubic meters, covering capacities
suitable for farms with 75 to 215 heads to feed in a single pass. These models have two vertical augers,
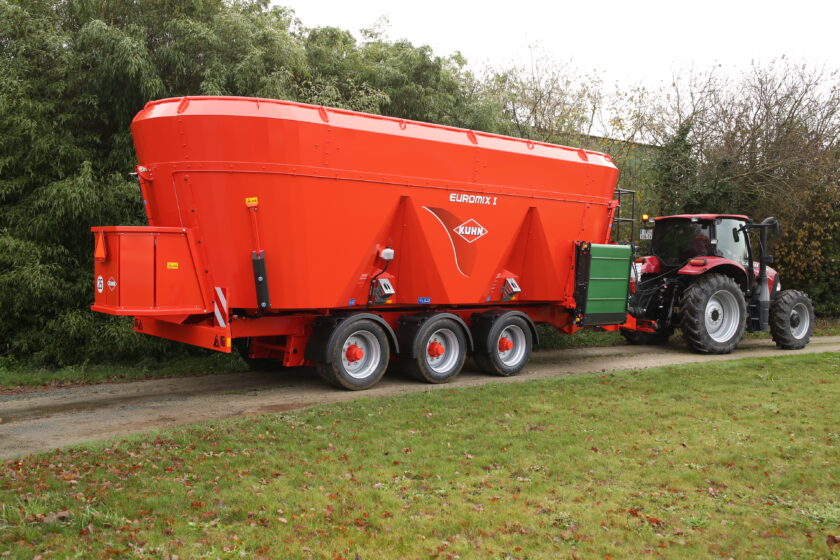
unlike the larger capacity trailed wagons, such as the “EuroMix” series, which operate three augers in their
tanks, ranging from 28 to 45 cubic meters in capacity. Naturally, the volumes of the tanks vary accordingly,
ranging from a minimum of nine cubic meters in the “Profile” and “Euromix” towed models to the top-of-
the-line model with 45 cubic meters.
Thanks to the “EuroMix”, even medium-small companies can benefit from modern and efficient equipment
while respecting their budget constraints and leveraging the tractors in their machine fleets. The latter are
left free to perform other activities if the company can invest in the self-propelled “Spw Intense” series,
specialized machines with high productivity propelled by Volvo six-cylinder engines calibrated to ensure
linear torque curves and generous power starting from low speeds, while consuming about ten percent less
fuel than industry averages. These engines provide approximately 250 horsepower, most of which are used
to drive the two-meter wide unloading augers. In the models with 14, 16, and 18 cubic meters, the power
absorbed by the augers is 160 horsepower, while 200 horsepower is required to drive the augers of larger
self-propelled models. In fact, the silage and mixing phases are the most demanding for the machines,
prompting Kuhn to address mixing by also varying the number of knives proposed by the augers, five in the
four larger models and six in the three smaller models.
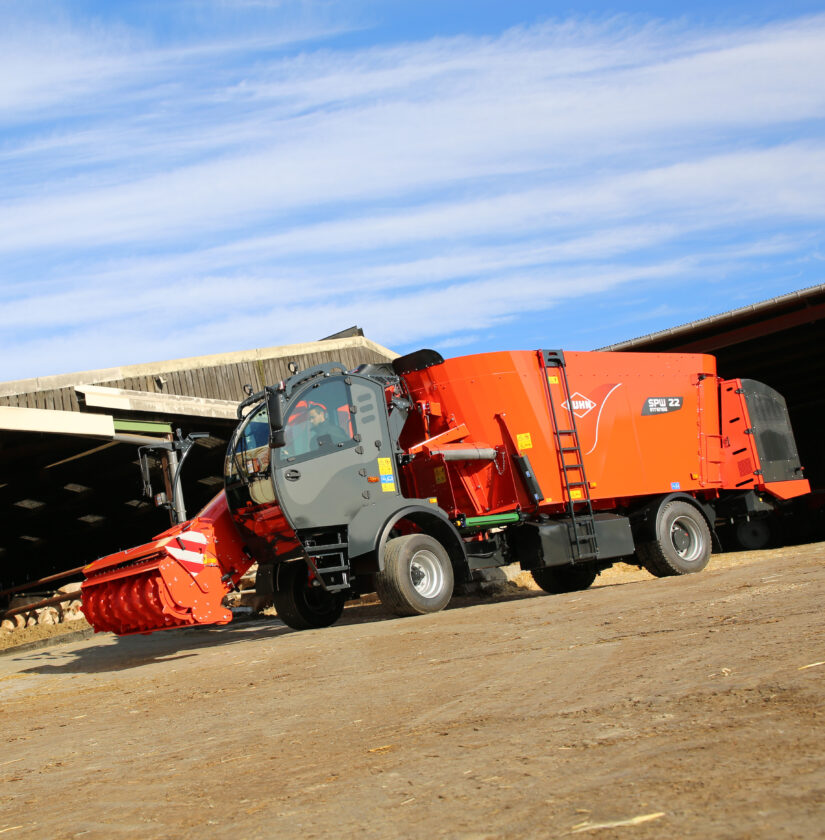
The efficiency and precision of silage and mixing are also enhanced by an electronically controlled pilot
system that automatically adjusts the rotation speed of the augers according to the forage density in the
trench, ensuring that only the minimum necessary layer is milled to create the most homogeneous front
possible. This aims to minimize the scalloping of the trench front to reduce the exposed area to air and
consequently its oxidizing action on the silage itself. Kuhn wagons operate with surgical precision in milling,
a characteristic that makes them particularly suitable for intensive use in large farms, where operational
efficiency translate into time and money savings.
However, to achieve this result, it is not enough for the machines to perform well in terms of silage and
mixing. They must also be characterized by high manoeuvrability and dimensions that allow them to access
inside barns. The “Spw Intense” models meet these requirements by offering maximum heights ranging
from 2.74 meters at the entry level to 3.46 meters in the top-of-the-range model. The widths are the same
in all seven models, the classic two and a half meters that allow circulation on the road if necessary, while
the lengths vary slightly, being just under ten meters in the first three models of the series, remaining
below 11 meters in the four higher models.
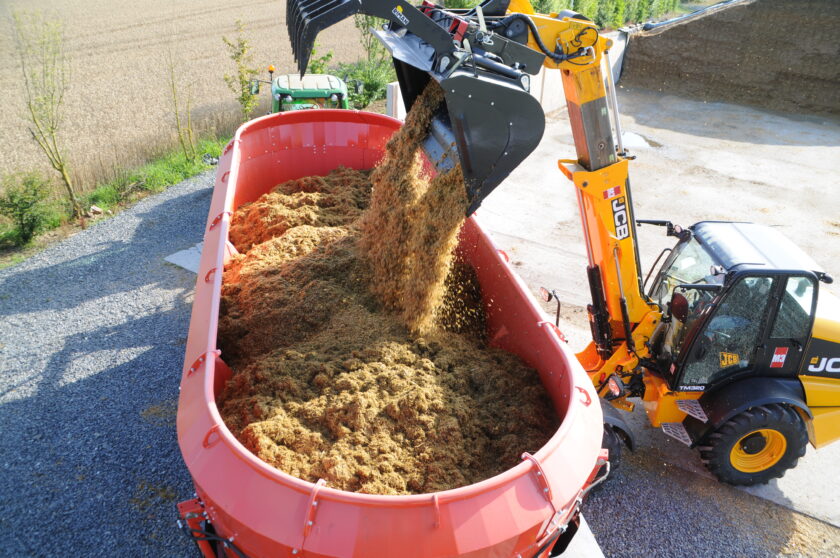
Ease of driving and maneuverability is emphasized by the
presence of both hydrostatic transmissions with two ranges, the longest of which allows a maximum speed
of 25 or 40 kilometers per hour, and integral steering systems that allow turning radii of less than seven
and a half meters, while the rear placement of the engine favors safety and stability by perfectly balancing
the distribution of masses on the two axes as the vehicle proceeds at full load.
Also noteworthy is the 300-millimeter ground clearance, which ensures easy overcoming of any bumps
present on the thresholds of barn entrances and exits, as well as the presence of maintenance-free drive
shafts, activated hydromechanically. Finally, specific retractable and reversible conveyor belts extend over
two and a half meters towards the housing areas to distribute the forage on the ground once the necessary
lengths have matured, operating at two different rotation speeds of the augers, 15 or 50 revolutions per
minute, and capable of unloading on both sides of the machine.
Top of the line comfort and visibility
In addition to their operational performance, the “Spw Intense” stands out as true category flagships
thanks to the “VisioSpace” cabins available in three different configurations: “Standard,” “Edition,” and
“Attractive.” A common feature is the excellent soundproofing and the unique design of the windows,
providing operators with maximum visibility in the working area, enhancing comfort and ensuring a higher
level of operational safety. With a specific design, the machine offers a twenty percent increase in overall
visibility compared to industry standards, along with excellent access to the compartment. The seats are
cushioned and integrate the primary controls of the machine into the right armrest, along with a
multifunctional joystick that facilitates control of various procedures.
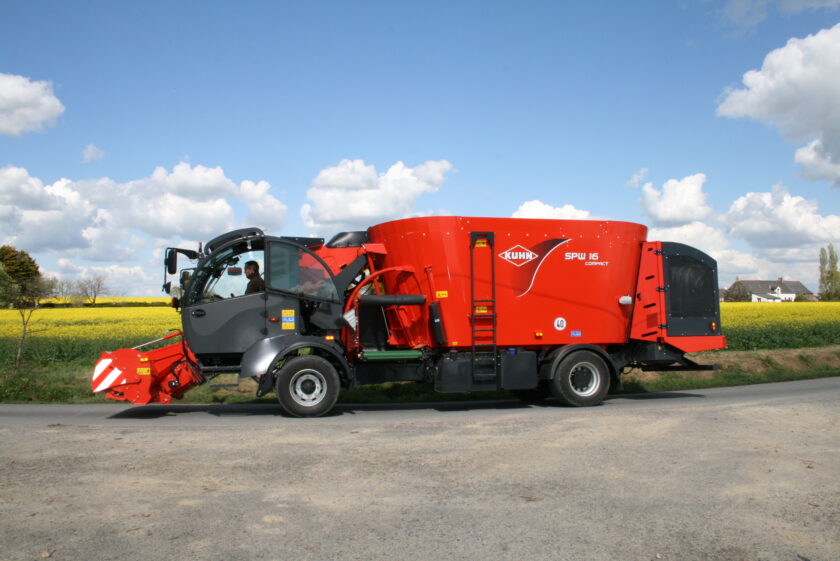
Also located to the right of the
operator is a Kuhn “Cci” series terminal, allowing the programming of work tasks by storing a large number
of recipes that can be easily recalled. Once a recipe is selected, a control and weighing system assists the
driver in gathering ingredients and properly controlling their mixing. A technological highlight is the rapid
defrosting system for the windshield, accelerating work startup during colder seasons. This system is
complemented by a windshield cleaning system operated by two brushes installed on a 1400-millimeter-
long movable arm, which can be aided by three nozzles for detergent spraying. The cabin is naturally
heated and cooled to ensure the operator’s preferred climate regardless of external temperature, and it
also offers the possibility of connecting with the company’s technical department if needed.
For those who prefer trailed wagons
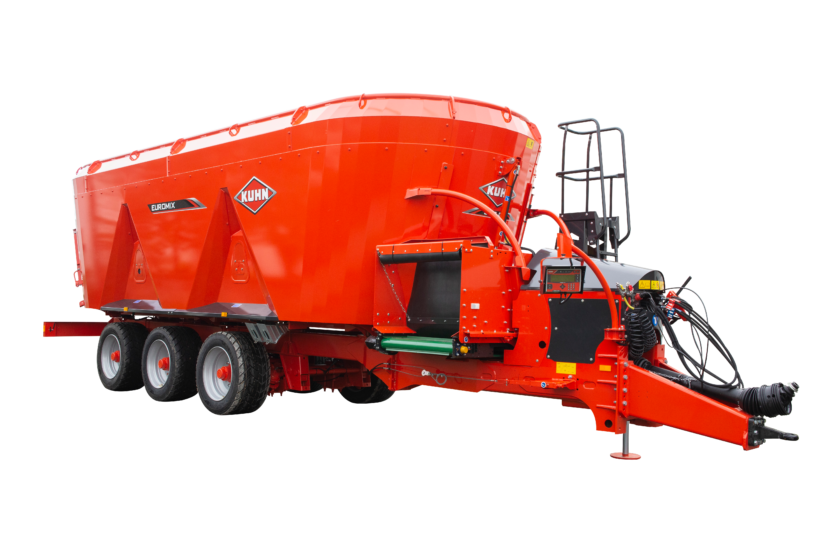
As mentioned in the main article, Kuhn also offers a series of trailed wagons called “EuroMix,” covering a
wide range of volumes from a minimum of 28 cubic meters to a maximum of 45. This caters to various farm
needs, including those of larger farms requiring significant feed distribution. For them, Kuhn proposes two
specific wide-tank machines equipped with triple augers, distinguished by the initials “Dl” and “Cl,” with the
former indicating a lateral distribution system and the latter a transversal distribution conveyor belt. Both
are perfect solutions for feeding herds ranging from 140 to 360 head, with four models available in
capacities of 28, 33, 39, and 45 cubic meters, facilitated by a steerable tridem axle that assists the tractor in
turning. These high-end machines, due to their large mixed and distributed masses, are equipped with six-
point weighing systems to ensure maximum accuracy in loading and unloading quantities. For the same
reasons, the tank’s geometry has been designed to simplify and make loading phases more precise and
secure, with specific configurations of the upper part of the tank and optional reinforced edges to protect
the tank itself in case of accidental impact. The polygonal design of the tank also contributes to increased
resistance to mechanical stress, especially during cutting of whole bales, aided by diagonal counter-knives
positioned relative to the vertical axis of the auger and connected at the top. This reduces the space
between the counter-knives and the auger, increasing contact surfaces with the forage. The knives are
asymmetrical for self-cleaning effects and ensure progressive and clean cuts. Another advantage is the use
of a high-strength steel alloy called “K-Nox” for making the augers, ensuring maximum wear resistance.